Plasma arc cutting can be used to cut stainless steel with a thickness of 3.0 to 80.0 mm. The cut surface is oxidized, and due to the characteristics of the plasma, the cut is in a figure eight shape.
Plasma arc cutting is to pass a mixed gas through a high frequency arc. The gas can be air or a mixed gas of hydrogen, argon and nitrogen. The high-frequency arc “decomposes” or ionizes some gases into basic atomic particles, thereby generating “plasma”. Then, the arc jumps to the stainless steel workpiece, and the high-pressure gas blows the plasma from the torch burner with an exit velocity of 800-1000 meters per second (about Mach 3). In this way, combined with the high energy released when the various gases in the plasma return to a normal state, a high temperature of 2700°C is generated. This temperature is almost twice the melting point of stainless steel. So that the stainless steel melts quickly, and the molten metal is blown away by the jet of high-pressure airflow. Therefore, it is necessary to use smoke and slag removal equipment.
The plasma arc is used as the heat source, and the thermal cutting is formed by melting and blowing off the molten metal by means of high-speed thermionic gas. The working principle of plasma arc cutting is similar to that of plasma arc welding, but the power supply has a no-load voltage of more than 150 volts, and the arc voltage is also as high as 100 volts. The structure of the cutting torch is also thicker than that of the welding torch and requires water cooling. Plasma arc cutting generally uses high-purity nitrogen as the plasma gas, but argon, argon nitrogen, argon hydrogen and other mixed gases can also be used. Generally, shielding gas is not used, and sometimes carbon dioxide can be used as a shielding gas.
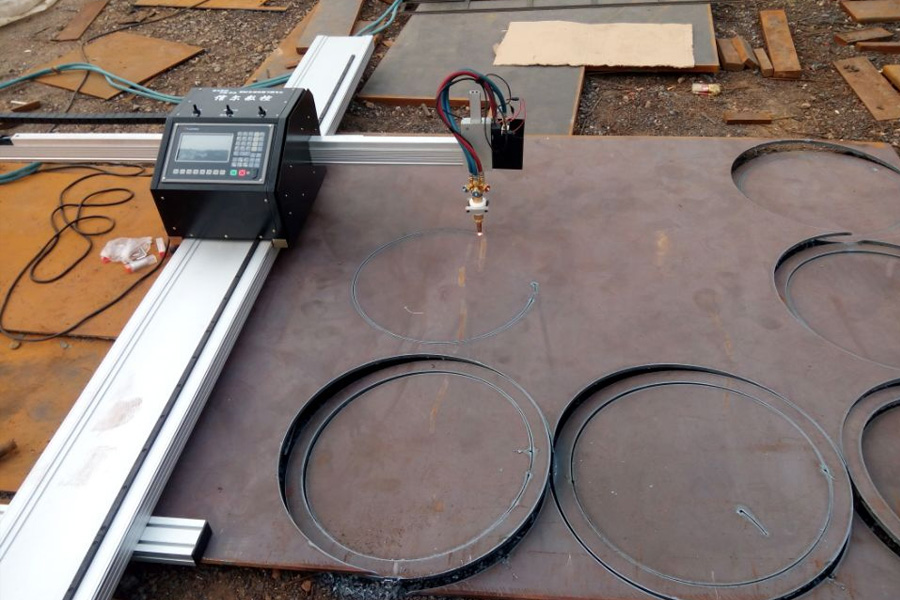
Classification of plasma arc cutting
There are 3 types of plasma arc cutting: low current plasma arc cutting uses 70-100 amperes of current, and the arc is a non-transferred arc, used for manual cutting of 5-25 mm thin plates or casting grooving, punching, etc.; high current plasma arc cutting When using a current of 100 to 200 A or more, the arc is mostly a transfer arc (see plasma arc welding), which is used for mechanized cutting or profiling of materials with large thickness (12 to 130 mm); water jet plasma arc cutting uses large Electric current, the outer jacket of the cutting torch is equipped with an annular water spray nozzle, and the sprayed water cover can reduce the smoke and noise generated during cutting, and can improve the quality of the cut.
Plasma arc can cut stainless steel, high alloy steel, cast iron, aluminum and its alloys, etc., and can also cut non-metallic materials, such as ore, cement board and ceramics. The incision of plasma arc cutting is narrow, smooth and straight, and the quality is similar to that of precision gas cutting. Under the same conditions, the cutting speed of plasma arc is higher than that of gas cutting, and the range of cutting materials is wider than that of gas cutting.
Advantages of plasma arc cutting
Plasma arc cutting is an ideal cutting heat source. Plasma arc cutting has the following advantages:
- (1) Wide application range. Plasma arc can cut all kinds of metal limbs from the melting point. Other cutting methods cannot cut metals, such as stainless steel, heat-resistant steel, titanium, molybdenum, tungsten, cast iron, copper, aluminum and aluminum alloy. The thickness of cutting stainless steel and aluminum can reach more than 200mm .
- (2) Fast cutting speed and high productivity. Among the various cutting methods currently used, the plasma arc cutting speed is relatively fast and the production firmness is relatively high. For example, cutting 10 ram aluminum plate, the cutting speed can reach 200-300m/h; cutting 12mm thick stainless steel, the cutting speed can reach 100-130m/h.
- (3) High cutting quality. When plasma arc cutting, a relatively narrow, smooth, neat, non-sticky, close to vertical incision can be obtained, and the deformation and thermal influence of the incision are small, and the hardness change is not large, and the cutting quality is good.
Plasma arc cutting parameters
The choice of plasma arc cutting parameters is critical to the effect of cutting quality, cutting speed and efficiency.
1. Cutting current
Cutting current is the most important cutting parameter, which directly determines the thickness and speed of the cutting, that is, the cutting ability. The cutting current increases, the arc energy increases, the cutting ability increases, the cutting speed is fast, the arc diameter increases, and the arc becomes thicker, which makes the incision wider. Excessive cutting current will increase the thermal load of the nozzle, and the nozzle will be damaged prematurely, and the cutting quality will naturally decrease, and even normal cutting cannot be performed. Therefore, the cutting current and the corresponding nozzle should be correctly selected according to the thickness of the material before cutting.
2. Cutting speed
Due to the different factors such as material thickness, material, melting point, thermal conductivity, and surface tension after melting, the selected cutting speed is also different. A moderate increase in the cutting speed can improve the quality of the incision, that is, the incision is slightly narrower, the surface of the incision is smoother, and the deformation can be reduced. The cutting speed is too fast to make the cutting heat input lower than the required value, and the jet in the slit can not blow off the melted melt immediately to form a large back drag. Accompanied by incision dross, the surface quality of the incision decreases.
3. Arc voltage
Plasma arc cutting machines usually have higher no-load voltage and working voltage. When gases with high ionization energy such as nitrogen, hydrogen or air are used, the voltage required to stabilize the plasma arc will be higher. When the current is constant, the increase of the voltage means that the arc enthalpy is increased, while reducing the diameter of the jet and increasing the flow rate of the gas, a faster cutting speed and better cutting quality can be obtained. The no-load voltage is 120~600V, and the arc column voltage cannot exceed 65% of the no-load voltage, generally half of the no-load voltage. At present, the no-load voltage of commercially available plasma arc cutting machines is generally 80-100V.
Link to this article:Plasma Arc Cutting - What Is Plasma Arc Cutting
Reprint Statement: If there are no special instructions, all articles on this site are original. Please indicate the source for reprinting.:Cut Wiki,Thanks!^^