Stone sawing mining refers to the use of various sizes of stone masonry, mechanical sawing, wedging, and blasting to cut the rock into a certain shape and size, which is used as the masonry and facing of civil construction projects. The method of separating blocks from the decoration materials and separating them from the rock mass.
The method of cutting the rock into a certain shape and size by means of mechanical sawing, wedging and blasting, and separating it from the rock mass. The quarried rocks are used as blocks for masonry and decorative materials for civil construction projects. Stone has been used in civil construction projects for thousands of years. The pyramids in Egypt, the foundations, step stones and railings of the Forbidden City in Beijing, China, and the stone archways of the Ming Tombs are all made of stone blocks of various sizes. However, the formation of a complete stone industry system only has a history of more than a hundred years. In modern times, various emerging building materials (such as cement, etc.) have replaced stone in a large range, but some permanent buildings, important public and social activities buildings, still need a large amount of natural stone as decoration materials and walls material. For example, China’s Yunhua, White Marble, Dandong Green and Hangzhou Grey, Italy’s Sina Golden Marble, and African Blue Granite are all best-selling products in the international market, and their demand continues to grow.
The magmatic rocks that can be used as structural or decorative materials include granite, andesite, trachyte and diabase; sedimentary rocks include limestone, dolomite, tuff, claystone, sandstone and shale; metamorphic rocks include marble, slate, etc. .
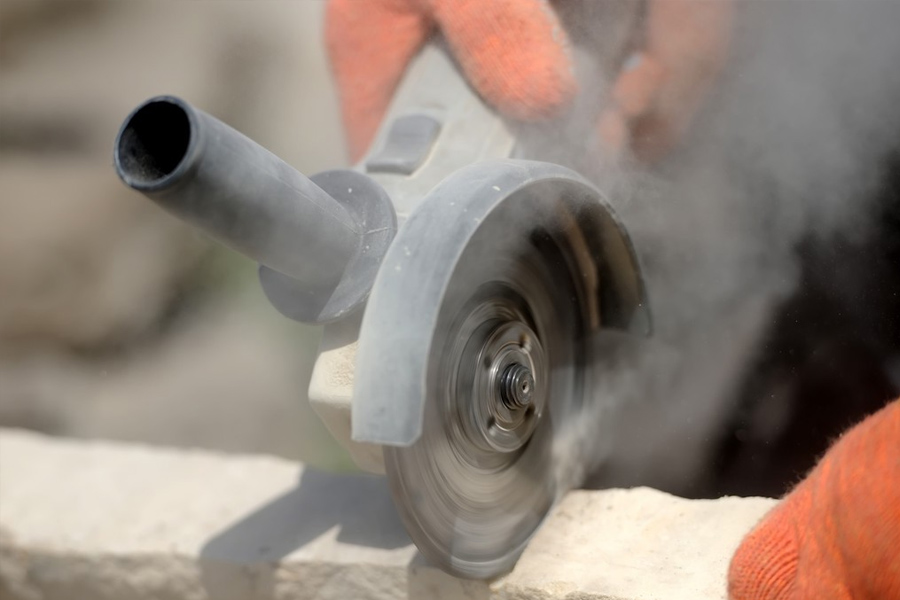
The height of the stoping steps mainly depends on the type of lifting equipment. It is generally 5-10m when using a mobile crane, and generally up to 10m or more when using a fixed tower crane. Large-scale equipment can save the amount of development and preparation engineering, so that the height of the steps has a tendency to increase. The height of the sub-steps of a sawing is mainly determined by the specifications of the column and its drilling device, which is generally 2~3m. The disadvantage of wire rope saws is that the cutting pressure is not high. Recently, vibrating wire rope saws have been used, and the production capacity can be increased by 32-40% compared with the stable transmission. Italy and the Soviet Union have begun to use diamond wire saws.
The flame cutting method uses the flame of a flamethrower to burn the rock to form a cutting surface to divide the rock. It is only used to recover rocks with more quartz minerals. It can only be cut vertically, and the loss of the cutting trench is large. In the case of three free surfaces , Generally cut two faces at most, it is best to cut only one face, and the other two faces are separated by blasting or wedge splitting. The surface to be cut by flame should be selected on the “section” and “astringent surface” that are the most difficult to separate. The noise in the production process is as high as 120dB, which is very harmful to the environment and workers and is rarely used.
Stone Sawing And Mining
Most of the stone is quarried in the open pit, and the amount of stripping works is not large. The method of deposit development is mainly without trench development. The stoping process includes separation, decomposition, trimming, lifting and loading. Separate big rocks of tens to hundreds of cubic meters from the rock mass, break the big blocks into square blocks, repair and reshape them, and lift and load the trucks. The salient feature of the stone recovery process is to make full use of the structural features of the rock. For example, sedimentary rocks are mainly bedding structures and suture structures and fractures; magmatic rocks are joints, flow surfaces, streamlines and rhyolite structures; metamorphic rocks are schistoscopy and massive structures.
The key to reducing the cost of stone production is to ensure the quality of the stone, increase the yield of the plate, reduce the mechanical workload and improve the efficiency of mining. The layout of the working face is mostly parallel to the direction of the cracks or joints; the height of the stoping layer is mainly determined by the bedding or the distance of the cracks. Stone recovery methods include split wedge method, blasting method, row drilling method, mechanical sawing method, flame cutting method and their combined methods.
Splitting the wedge method to drive a metal wedge along the rock structure surface, or use a rock drill to drill a wedge hole, use a hydraulic splitting machine to drive a wedge to split the rock, separate a certain volume of rock from the rock mass, and split it into smaller pieces Regularize blocks.
The blasting method is used in the separation process of the rock. After separation, the rock is decomposed and trimmed by sawing. The blasting method is divided into ordinary blasting, pre-split blasting and silent blasting. The horizontal area of the rock separated by ordinary blasting can range from hundreds to 2,000 square meters, and the efficiency is higher than that of the split wedge method, but excessive rock fragmentation and hidden damage (microcracks) often occur, and the yield of block materials only accounts for 25 to 35 of the blasting volume. %, the board only accounts for 5%, and the strength of the stone is reduced, and it can be reduced to half of the original strength in severe cases. Pre-split blasting has improved this. Silent blasting has been widely used in the 1970s. The crushing agent is mixed with water and then filled into dense blastholes. The volume of the mixed liquid expands to crack the rock. The price of this type of crushing agent is 50% lower than that of explosives, and it is safe and silent, and the rock is not damaged by vibration. The blasting method and the split wedge method are only suitable for rocks with structural surfaces.
Row drilling method Use a rock drill to pierce small holes (below 40mm) to separate rocks. This method requires the drilling direction to be consistent and strictly parallel. It is suitable for the condition that the rock has a horizontal structural surface (bedding), and the rock can be cut off by only drilling a vertical borehole. The row drilling method is often used in conjunction with the split wedge method or blasting method, or used for rock decomposition. Due to the large workload and energy consumption of rock drilling, it is generally used for granite, basalt and other hard rocks that are difficult to mechanically saw.
Mechanical sawing method Use various mechanical saws to cut the rock directly to separate it from the parent rock. The mechanical saws used include chain saws, circular saws or circular saws. Disc saws and wire rope saws are mainly used to recover square wall materials, and chain saws and wire rope saws are mainly used to recover facing stone. The mechanical saw is only suitable for mining sedimentary rocks and metamorphic rocks such as marble, limestone and tuff with low hardness. Among them, chain saws and circular saws have poor adaptability to hard nodules, and are generally used for rocks with pressure less than 12kN/cm2 and quartz content less than 5%. The wire rope saw has strong adaptability, simple equipment structure, light weight, convenient and flexible movement along the working surface, and is widely used.
The chain saw uses a cutting disc rotating mechanism to perform horizontal and vertical cutting. It needs to walk on the track to keep it stable. The working surface is step-shaped, and the height and width depend on the size of the cut-off disc, generally 2~3m, and the length of the working surface is 100~150m. When cutting marble with a chain saw, if the cutting seam is 2m deep, the pure cutting speed can reach 35~75mm/min. The chain saw cannot cut vertically. When there are only 2 to 3 exposed surfaces, it needs to be combined with blasting, drilling, and wedge splitting. The most ideal method is to use a chain saw to cut the bedding surface vertically, and use the split wedge method to separate along the bedding surface.
Circular saws are most commonly used in the Soviet Union. The sawing depth is 35-40% of the diameter of the saw disk when the drive shaft is in the center of the saw disk, and 70% when the saw ring is driven by a gear. It is mainly used for sawing small wall materials, that is, directly sawing into blocks in the quarry.
Wire rope saws were first created in Italy in about 1895 and are now widely used in various countries. Driven by a drive drum to drive a three-strand wire rope with a diameter of 3.5-5mm and a length of about 1000-2000m, leading to the sawing working surface through a number of guide wheels and working columns, and adding water and abrasives to the planned sawing surface, generally natural quartz Sand or silicon carbide sand, the abrasive is driven by the wire rope to grind the rock, gradually forming a saw cut, and finally sawing the rock (see picture). The wire rope running speed is generally 8-10m/s, and the highest can reach 14m/s. When sawing marble with a length of 20m, the sawing efficiency is 0.8-1m2/h. The wire rope saw can be cut vertically or horizontally. When the working column is equipped with a drilling device, the work surface preparation and separation sawing can be completed separately.
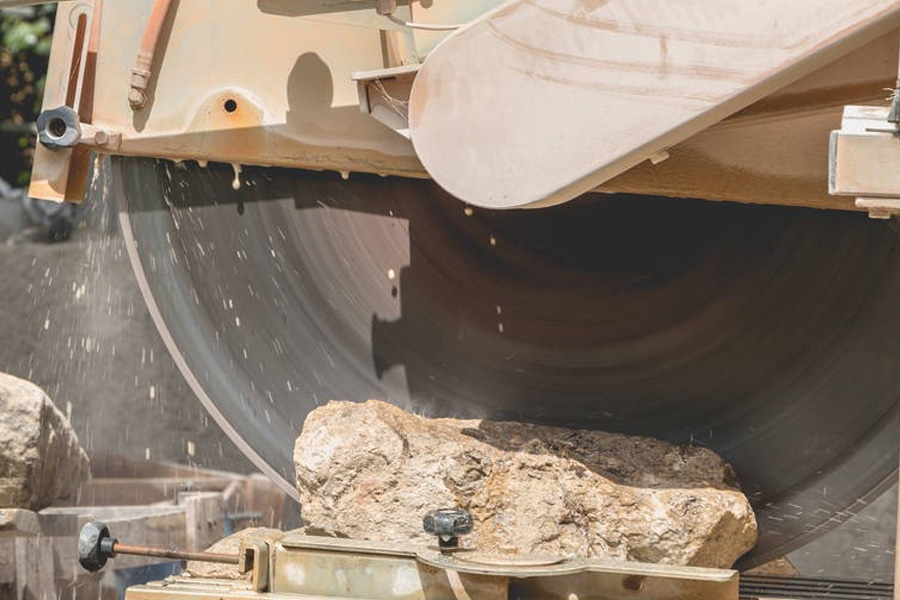
Link to this article:Stone Cut - What Is Stone Cutting
Reprint Statement: If there are no special instructions, all articles on this site are original. Please indicate the source for reprinting.:Cut Wiki,Thanks!^^