1 Reasons for the sticking of die castings
The hazards of sticking mold defects to castings are: when the die castings are stuck to the mold, the lighter surface is rough, which affects the roughness of the appearance; the heavy casting surface peels, lacks meat, strains, and cracks, and can also cause castings to leak, resulting in castings Scrap in batches. There are many phenomena of die-casting sticking, and the basic reasons for sticking are as follows.
1.1 The affinity of die-casting alloy and die steel
The greater the affinity between die-casting alloy and die steel, the easier it is to melt and bond with each other. After the die-casting alloy is bonded to the mold wall, there will be greater demolding resistance, and the casting will be strained when demolding. Visually observe that there are drawing traces such as rough surface, peeling or lack of material at the sticking part of the casting (note: to be distinguished from carbon deposit), and the casting will be torn and damaged in the case of severe adhesion. The surface of the mold cavity is visually adhered to a laminated casting alloy, and the color is white.
After the injection or flow of the die-casting alloy liquid impacts the mold wall or core, the temperature of the mold wall or core increases. At high temperatures, the alloy liquid and the mold steel of the mold wall melt and weld together to cause mutual adhesion. The higher the alloy liquid temperature, the higher the injection speed, the higher the mold temperature and the lower the mold hardness, the higher the affinity between the aluminum alloy liquid and the mold steel, the more likely it is to melt and weld adhesion. When the die surface adhered to the die casting alloy is demolded, the cavity surface and the casting surface are squeezed and torn, which will tear the surface of the casting, and the surface of the casting will appear sticky mold strain.
The higher the filling speed of the die-casting alloy liquid in the inner runner, the more severe the impact of the molten metal flow on the mold wall. The molten metal directly impacts the core or wall, and the impact force is converted into heat energy. Not only the temperature of the alloy liquid will rise, but the temperature of the mold at the impacted part will also rise a lot, which greatly increases the affinity between the aluminum alloy liquid and the mold steel. Therefore, mold sticking is most likely to occur in the part of the runner in the mold that is subject to the high-speed impact of the alloy liquid. If it hits the side of the fixed mold, the packing force of the casting on the side of the fixed mold is increased.
The hardness of the mold is insufficient, and the mold surface during demolding will be squeezed and deformed by the die-casting alloy, or the mold core will be bent and deformed, thereby increasing the mold’s resistance to demolding of the casting.
Improper use of mold materials, when the mold temperature is high, the die-casting alloy easily adheres to the surface of the mold.
1.2 Demoulding angle
Mold demolding slope is too small (or no demolding slope, or reverse demolding slope), the side of the mold is uneven (erosion, crushing, defect, etc.), the surface is rough, etc., and the casting is hindered in the demolding direction . The surface of the casting is strained by the mold when the casting is demolded, and the surface of the casting shows linear strain marks along the mold opening direction, that is, the scars at the beginning of the deep cavity of the casting are wide and deep, while the scars at the end of the mold gradually become smaller or even disappear. Strain the whole face.
- (1) The mold design and manufacture are not correct, and the demoulding slope of the fixed mold cavity or core forming surface is too small or has a reverse slope, which makes the casting resistance to demoulding very large. For the parts that require no demoulding inclination of the casting, it is best to leave a machining allowance for the casting to make the demoulding inclination, and then let the parts without demoulding inclination of the casting be finished afterwards.
- (2) The crushing deformation on the mold core or the mold wall and the protrusion on the side of the cavity will affect the demolding of the casting, and the scratches on the forming surface or the mold cracking will also affect the demolding of the casting.
The fixed molding surface of the mold is too rough, or has traces of processing and manufacturing, is not smooth enough, or the lines of the processing and polishing traces are inconsistent with the demolding direction, or the flatness in the demolding direction is poor, such bad surfaces will increase due to The demolding resistance hinders the demolding of the casting, causing the surface of the casting to have traces of polishing or scratching. Such scratch marks are linear grooves in the demolding direction, the shallow ones are less than 0.1 mm, and the deep ones are about 0.3 mm.
1.3 The tightness of the casting to the mold
The overall or local shrinkage of the casting has too much clamping force on the mold, or the distribution of the clamping force is unbalanced and unreasonable. At this time, the casting will be deformed, cracked, or broken due to the sticking of the mold, and even the casting will stick to the fixed mold. Or there may be a phenomenon that the casting sticks to the top of the movable mold and cannot come out.
- (1) The overall or partial packing force of the casting to the fixed mold is greater than the packing force to the movable mold, and the casting will stay stuck when the mold is opened.
- (2) During demolding, if the tightening force of each part of the casting on the moving and fixed molds is not uniform, the casting will be deflected, skewed, and skewed when it is pulled out, and the part of the casting with a large tightening force on the fixed mold will be affected. It may stick to the fixed mold.
- (3) If the temperature of the fixed mold is too low or the temperature of the movable mold is too high, the packing force of the fixed mold will be greater than that of the movable mold when the casting shrinks.
- (4) The concentration of mold release agent is too low, the release performance of the release agent is not good, the release agent sprayed on the fixed mold is not in place, and the amount of release agent is insufficient, which will affect the release performance of the casting. If too much paint is sprayed on the fixed mold during the hot mold, the temperature of the fixed mold is difficult to increase rapidly. After the casting cools and shrinks, the tightening force on the fixed mold side will increase more than the movable mold.
- (5) There is also a phenomenon of mold sticking: in the first period of die-casting production, that is, when the hot mold is injected at a low speed, the fluidity of the die-casting alloy liquid will drop rapidly due to the low mold temperature, resulting in filling The molten metal forming in the cavity is very incomplete, the strength of the formed casting is very low, and the connection between the various parts of the casting is very weak. When the casting is demolded, the part with greater tightening force will easily break with other parts. Separated and stuck in the mold. In particular, there is no ejector pin on the side of the fixed mold to eject the casting, so it is easier to stick to the fixed mold.
For the sticking phenomenon that occurs every time during die-casting, the reasons for its occurrence should be analyzed in detail. For example, if the casting sticks to the fixed mold during die casting, it is necessary to check the reason for the excessive tightening force of the casting on the fixed mold; check the appearance of the fixed mold side of the casting, follow the demolding direction, and there are traces of the die on the surface of the casting. When the sticking mold is severely scratched or scratched, there will be a large demolding resistance, which will make the part of the casting or the entire casting not come out in the cavity, and the casting will stay stuck and cause sticking; in severe cases, not only the casting will be torn and damaged The phenomenon of strains, cracks, and fractures may also occur in the core and cavity of the mold. The sticking phenomenon of die castings is most common in aluminum alloys. The specific measures to solve the sticking defects of die castings are as follows.
2 Measures to prevent castings from sticking to the fixed mold
2.1 Measures to prevent castings from sticking to fixed molds in die casting molds
In the trial mold of the newly produced mold, or when the die-casting production starts the hot mold, the phenomenon of die-casting sticking often occurs. When the die-casting operation process is normal, the main reason for the sticking of the castings is not the die-casting process, but should be the problem of the casting structure design, mold design or manufacturing. Although the die-casting process and spraying debugging can be remedied, the remedial effect is general and not very stable, and the phenomenon of casting sticking will still occur.
If the casting is prone to stick to the fixed mold, the mold should be preheated well before die-casting, and the mold cavity should be coated with anti-sticking mold paste and compressed air before starting low-speed injection. Blow evenly, apply once for each die-casting mold, try die-casting about 20 molds, if the mold is still fixed, it means that the mold has a problem and needs to be repaired.
For the castings that have been designed, it is true that the clamping force of the casting to the fixed mold is greater than the clamping force to the movable mold. It is necessary to allow the casting to be set on the side of the fixed mold to eject the casting, and to allow the surface of the casting on the side of the fixed mold. Leave the ejector marks, or make the ejector marks easy to remove. In this way, when designing the mold, the ejection mechanism of the casting should be designed on the side of the fixed mold.
Pay attention to the calculation of the packing force of the moving and fixed molds. For castings whose packing force of the fixed mold is greater than the packing force of the moving mold, or for the castings with the packing force of the fixed mold and the moving mold similar to that of the movable mold, it is possible to stick The fixed mold may stick to the casting of the movable mold. When designing the casting or mold, it is necessary to change the structure of the casting or mold, the draft angle, the surface roughness, etc., and try to make the casting force of the movable mold greater than The tightening force of the fixed mold.
For castings with a relatively large packing force on one side of the fixed mold, when designing a new mold, the parting surface should be selected as far as possible on the side that is biased to the fixed mold, and the castings should be placed in the moving mold cavity as much as possible to increase the pairing of the castings. The tightening force of the movable mold. In order to reduce the tightening force on the fixed mold, it is necessary to re-determine the demolding slope of the fixed mold with the casting designer, and the demolding slope of the fixed mold should be increased as much as possible; pay special attention to correcting or increasing the casting on the side of the fixed mold. The demolding slope of the part that is strained by the mold sticking to the mold. At the same time, appropriately reduce the demolding slope of the movable mold; pay special attention to correcting or reducing the demolding slope of the movable mold near the ejector pin. Try to set the core on the movable mold, or increase the length of the core on one side of the movable mold.
It is necessary to prevent the fixed mold from producing undercuts or rough surfaces that affect the demolding during manufacturing and polishing; after the mold trial or during the die-casting process, it is necessary to correct the deformation of the fixed mold cavity from crushing and bruising; use polishing or chemical cleaning agents to eliminate the alloy If the adhesion marks on the surface of the fixed mold and the alloy adherents on the mold are not removed in time, the sticking phenomenon will become more and more serious after a long time; better polish the rough surface of the side wall of the fixed mold cavity. But after the fixed mold is polished into a mirror surface, it is not conducive to the adhesion of the paint. When the mold is opened, a tight vacuum gap will occur between the casting and the mold, which increases the demolding resistance, so the bottom of the fixed mold deep cavity can not be polished into a mirror surface. . For molds that have been nitrided, polishing should be done carefully to prevent damage to the nitrided layer on the surface, and prevent the more polished, the more the mold will stick.
Modify the mold runner, appropriately change the position, size and filling flow direction of the runner to eliminate or reduce the erosion and mold sticking defects caused by the impact of the runner on the fixed mold. For example:
- ①Change the filling flow direction of molten aluminum to minimize the violent impact of molten metal on the fixed mold cavity. You can change the direct impact of molten metal to face the core or wall obliquely;
- ②Appropriately increase the cross-sectional area of the inner runner. In order to reduce the flow rate of the molten metal in the inner runner;
- ③Change the position of the inner runner, make the inner runner in the wide and thick position of the casting, and avoid the impact on the side wall of the fixed mold;
- ④Try to take the feed at the bottom of the deep cavity of the casting Method;
- ⑤Adopt an open runner, the bell mouth of the runner faces the cavity to enlarge the injection area;
- ⑥For the impact part or core of the runner, a tungsten carbide rod coating machine can be used to apply electricity to the surface of the mold.
The spark metallurgical method sprays the tungsten carbide microparticle layer, the metal tungsten particles and the base metal will not fall off, which can improve the anti-sticking property of the mold surface, such as depositing a 2 to 4 micron thick coating on the surface of the die-casting mold, and its hardness It can reach HV4 000~4 500, and the operating temperature can reach 800℃.
In order to pull the casting to the side of the movable mold, a wedge-shaped barb hook can be repaired from the head of the ejector rod (the hook length is 5-8 mm, and the casting part thickness is 1-2 mm, see Figure 1), so that the die-cast barb hook handles Pull the casting to the side of the movable mold, and then remove the barb hook on the casting. In order to increase the tightening force of the casting on the movable mold, the surface roughness of the corresponding mold parts can be increased for the parts that need to be finished on the casting and the side surfaces of the parts that do not affect the appearance quality, so as to increase the effect of the casting on the tightening force of the movable mold. More obvious.
In order to increase the tightening force of the movable mold, tension bars can be used appropriately (see Figure 2):
- ①In the case of not affecting the appearance of the casting, several grooves can be made on the side surface of the movable mold or the surface of the core, or several dents with a depth of about 0.1 to 0.2 mm can be ground in the mold. . But pay attention to that the hook groove should be opened near the ejector rod to prevent uneven ejection force;
- ②When opening the mold, if you want to use the runner to pull the casting to the side of the movable mold through the inner runner, you can repair the tension ribs on the side of the runner on the side of the movable mold, or grind a few depths of 0.2. ~0.3 mm concave point to increase the clamping force of the runner to the movable mold;
- ③You can also set the ejector pin on the runner near the inner runner, shorten the ejector pin to 5-8 mm lower than the mold surface, and trim the side where the ejector pin is 3 mm below the mold orifice to a width of 2 to 3 mm, an annular groove with a depth of 0.3~0.5 mm. The annular tension rib formed after die-casting drives the runner, and the runner pulls the casting to the side of the movable mold through the inner runner. Better results;
- ④If it is because the sprue bushing exerts a large tensile force on the cake and sprue, the casting is brought to the fixed mold, and the tensile ribs can be repaired on the side of the runner of the movable mold and the sprue of the split cone. When the mold is opened Pull the runner and the cake to the side of the movable mold with the tension bar;
- ⑤ For castings with relatively thick walls, or castings with inner holes that need to be finished, after reducing the demolding slope of the movable mold core, if the problem of the fixed mold cannot be solved, it can be in the middle of the core length A ring groove with a width of 2 to 3 mm and a depth of 0.2 to 0.5 mm is repaired to form a tension rib, and the ring tension rib pulls the casting to the side of the movable mold. Note that there must be at least 2 ejector pins to eject the casting near such a core to prevent the casting from deforming.
For the castings whose packing force on the fixed mold side is greater than the packing force on the movable mold side, in order to make the casting smoothly out of the fixed mold, the ejector plate, ejector rod and reset rod are designed to eject the casting like the movable mold. It is possible to add an oil cylinder or a spring on one side of the fixed mold to push the top plate and ejector rod on the fixed mold to eject the casting while opening the mold. There is a spring behind the ejector plate. When the mold is opened, the fixed mold ejector is ejected from the parting surface. When the mold is closed, the movable mold parting surface is used to push the four reset rods to push the fixed mold push plate and the ejector to reset.
In order to use the ejector rod to eject the casting from the fixed mold, the hook rod, impact block and roller mechanism similar to the three-plate two-part parting mold can also be used (see Figure 5, the casting, ejector rod and reset rod are not shown in the figure) , Relying on the mold opening action to drive the fixed mold ejector push plate to eject the castings from the fixed mold. The structure is as follows: Design the ejection structure of the ejector pin to eject the casting for the given mold, let the ejector plate 5 of the fixed mold extend out of the fixed mold model 6, and set four (or two) hooks on the movable mold 1. The four (or two) hook rods 4 extend to the side of the fixed mold 6 when the mold is closed. The hook rod 4, the impact block 7, the spring 3, and the roller mechanism 8 are used to make the four hook rods 4 and the fixed mold The top push plate of the mold is connected by a hook. When the mold is opened, the movable mold pull rod 4 hooks the fixed mold ejector pusher 5, and the fixed mold pusher pushes the ejector 5 to move the ejector rod to eject the casting from the fixed mold. At this time, the casting and the movable mold move synchronously. After moving to a certain stroke, use the impact block, roller, and spring mechanism to disengage the hooks of the four hook rods from the fixed mold ejector push plate, the fixed mold ejector push plate stops moving, and the movable mold parting surface is also used when the mold is closed. Push the four reset rods back to the fixed mold ejector push plate to make the fixed mold ejector return to its position.
2.2 Measures to prevent castings from sticking to the fixed mold in terms of die casting process
Spray coating on the mold, the flow impact velocity of the alloy liquid, and the mold temperature are the main factors that affect the sticking of the casting.
The variety, quality, concentration, spraying position, spraying time and amount of mold release agent affect the sticking condition of the casting Ⅲ. Use the amount of sprayed release agent to adjust the release effect of the casting on both sides of the moving and fixed molds. In order to prevent the casting from sticking to the fixed mold, the time and amount of release agent sprayed on the movable mold can be appropriately reduced. The paint sprayed on the movable mold should be thin and uniform, but the paint should not be missed. Increase the amount of release agent sprayed on the fixed mold to reduce the temperature of the mold surface, especially for the surface of the fixed mold strained castings and the surface with drawing marks, increase the amount of spraying. When there is no fixed position on the side of the fixed die, or there is no trace of the die, pay attention to appropriately increase the amount of coating sprayed.
On the surface of the mold with drawing marks, apply the anti-sticking mold paste before the paint is sprayed after the die-casting, so that the anti-sticking mold paste is sintered to the mold surface at a high temperature, so that a formation is formed between the alloy liquid and the mold surface A thicker diaphragm layer can play a better role in demolding.
Properly adjust and control the mold temperature. It is necessary to analyze the stress of the casting tightness and adhesion mold, the temperature difference of the mold and the shrinkage of the casting, and the relationship between the mold temperature and the alloy shrinkage and the tightness of the mold. If there is a sticky mold strain on the surface of the casting, try to use a lower mold temperature while ensuring the surface quality of the casting. If the casting itself has a large tightening force, try to use a higher mold temperature, which can reduce the shrinkage of the casting during demolding, that is, when the casting has not reached a large tightening force, it will begin to demold .
Relatively lowering the temperature of the movable mold and promoting the shrinkage of the casting can increase the tightness of the casting to the movable mold; relatively increasing the temperature of the fixed mold and reducing the shrinkage of the casting can reduce the tightness of the casting to the fixed mold. Increasing the flow rate of the cooling water of the movable mold can reduce the mold temperature of the movable mold; reducing or closing the flow of the cooling water of the fixed mold can increase the mold temperature of the fixed mold. Generally, for die-casting aluminum alloy castings, measure the surface temperature of the movable mold cavity within 1 to 3 seconds after opening the mold. The surface temperature should not be greater than 300℃, preferably (240±40)℃; and before closing the mold after spraying Measure the surface temperature of the fixed mold cavity within 1 to 3 seconds, and it should be no less than 140℃.
The pouring temperature, like the mold temperature, can change the shrinkage of the casting and the tightness of the packing. Increasing the pouring temperature and shortening the mold opening time can reduce the packing force, but will increase the affinity between the alloy liquid and the mold steel, and cause the possibility of sticking in the thick-walled part of the casting.
3 Measures to prevent castings from sticking to the moving mold
3.1 Measures to prevent castings from sticking to the movable mold in terms of die-casting molds
The main reason for the castings sticking to the movable mold is that the castings have too much tightening force on the movable mold, and the ejection force of the ejector rod is insufficient. If the ejection force is not large enough, it is necessary to increase the hydraulic pressure or ejection speed of the ejection cylinder of the die-casting machine. If the diameter of the ejector pin is too small, or the number of ejector pins is small, the strength of the ejector pin is not strong enough, and the ejector pin may bend or break.
If the force of the casting sticking to the movable mold is small, the strain is lighter when the casting is demolded, or the resistance caused by the rough surface of the mold is small, but the casting is deformed when it is ejected, and the mold sticking part should be polished, nitrided, or increased The amount of sprayed release agent reduces the release resistance. . If the casting force sticks to the movable mold is great, the casting is severely strained when the casting is demolded, the top of the casting is broken or disconnected, or the casting is ejected by the ejector, the casting angle should be increased appropriately. Improve the design of castings or molds, and eliminate unreasonable structures that cause castings to stick to molds and affect shrinkage.
In order to prevent the sticking mold strain caused by the uneven ejection force of the casting, the four push rods of the die-casting machine pushing the mold ejection plate must be the same in length, and the difference should not be greater than 0.20 mm; the machine push rod and the ejector The position of the ejector rod of the casting should be balanced and reasonable, and should not deviate from the center of the mold cavity, and should not deviate from the center of the ejector cylinder of the die-casting machine.
If the core-pulling and ejection settings are not balanced, the casting will be unevenly stressed and will be deflected. If the length of the push rod of the hydraulic ejection cylinder of the die-casting machine is not the same, the ejection force of the casting is uneven, or the position of the push rod is improperly arranged, the casting will be deflected during ejection. The improvement measures are: modify the mold structure, adjust the core pulling mechanism and the position of the ejector rod, so that the casting force is evenly ejected, and ensure that the casting is pushed out in parallel and evenly; adjust the ejection mechanism, the position and quantity of the push rod of the die casting machine (the most Easy to use 4-6 push rods) to make the ejector rods and castings of the mold evenly stressed; increase the number of ejector rods reasonably, increase the diameter of the ejector rods, and arrange the ejector rod positions to ensure the ejection balance.
If the deformation resistance of flat parts and thin-walled castings is insufficient, the number and diameter of the ejector pins should be increased. You can also add a small boss at the ejector position to let the ejector pin rest on the small boss of the casting. Large ejection force area makes the force of the casting uniform.
Use high-quality mold steel, so that when the mold temperature is high, the die-cast alloy is not easy to adhere to the surface. With high-quality mold steel, micro-cracks will not form prematurely on the mold surface, which also eliminates the basis of alloy sticking.
When the mold hardness is insufficient or brittle, the alloy liquid is prone to mold sticking. It is necessary to check whether the mold hardness is reasonable, and also to check the heat treatment process to prevent brittleness of the mold steel. The hardness of the modules, mold inserts and all cores that can withstand the impact of the inner runner are HRc3~5 higher than the hardness of the mold cavity module. When the mold design confirms that there is no problem, and the casting mold sticking strain is still difficult to eliminate, surface treatment measures such as nitriding, KANI 7C, tungsten coating, PVD nano titanium plating, etc. must be used to improve the surface hardness of the mold.
For the surface of the mold cavity, it is generally polished with oilstone and sandpaper. If you use a pneumatic tool to polish the sticking part, you must be careful not to damage the mold, so as not to damage the nitride layer on the surface of the mold, otherwise the more polished, the more sticky the mold will be. Case. When cleaning the non-cavity part of the sticky mold or sticky drape, you can use a spatula to remove the bumps, and then lightly polish with sandpaper. Do not scoop out the pits, otherwise it will cause more serious sticking. Be careful not to use chisel to clean the sticky mold in the mold cavity at any time, so as not to gouge the mold cavity.
3.2 Countermeasures to prevent castings from sticking to the moving mold in terms of die casting process
Reduce the high-speed injection speed of the die-casting machine, or increase the area of the runner in the mold to appropriately reduce the filling speed of the runner. If the area of the inner runner is increased without increasing the filling speed of the inner runner, the filling time can be shortened, the total heat generated by the impact of the inner runner can be reduced, and the effect of reducing the impact of the inner runner can be achieved.
Appropriately reduce the casting pressure: For thin-walled parts and castings without pore requirements, you can choose a smaller pressure, such as 40-55MPa; general castings choose 55-75 MPa; for thick-walled parts and castings with pore requirements, use a higher pressure , Such as 75~100MPa; when a large pressure must be used, 100~140 MPa can be selected. The higher the casting pressure, the better the mechanical properties of the casting, and the greater the tightness of the casting to the mold. If mold sticking occurs, it is necessary to confirm the use of appropriate casting pressure. Appropriately reduce the mold opening time (mold cooling time) so that the casting can be demolded at a higher temperature and the clamping force of the mold has not reached the maximum value, which can reduce the clamping force of the casting to the mold and reduce the sticking of the mold. degree.
If the demolding angle of the casting is too small, it is most likely to cause the casting to stick to the mold. Therefore, it is necessary to select a suitable demolding angle according to the alloy material and size structure of the casting. When mold sticking occurs, appropriately increasing the draft angle can eliminate the sticking phenomenon caused by thermal shock and shrinkage. If the casting structure is unreasonable, it will cause the shrinkage of each part of the casting to be uneven during the shrinking and cooling process, and the resistance to shrinkage is unbalanced. If possible and necessary, improve the design structure of the casting to make the wall thickness uniform, such as changing For the thickness of the section, try to design the thick parts as hollow structures or ribs connecting structures; avoid transition parts with large thickness differences; eliminate unreasonable bosses, lugs, and reinforcing ribs. Increasing the casting fillet or demolding angle at the concave corner of the casting can also prevent mold sticking.
In the vicinity of the inner runner of the mold and the part where the alloy liquid fills the impact cavity, the part of the mold with thick wall thickness in the casting, and the recessed corner of the casting, it is easy to be affected by the alloy liquid for a long time. Casting sticks and strains occur, so cooling water pipes should be provided for these parts of the mold for water cooling. For slender core cooling, the pressure of the cooling water should be increased. These can well reduce the mold temperature and prevent mold sticking.
If the die-casting alloy adheres to the mold surface at the surface of the casting, some small bubbles appear on the surface. For this phenomenon, the mold surface is polished with emery cloth and oil stone and the mold is repeatedly stuck again, which cannot completely solve the problem. A better way to solve this kind of sticking is to perform shot peening on the surface of the sticking mould, or to make the surface of the sticking part of the mould with a width of 0.2~0.5 mm and a depth of 0.2~0. The net pattern of 5 mm and the interval of 2 to 5 mm can eliminate the defects of sticking on the surface of the casting.
The shrinkage of the runner causes casting deformation and mold sticking. The length of the branch runner should be lengthened to reduce the area of the branch runner; the width of the runner should be reduced, the length of the runner should be lengthened, and the runner should be reduced. The number of channels; increase the cooling of the runners of the mold by the cooling water, so as to eliminate the influence of the shrinkage of the runners on the castings.
The less iron content of die-cast aluminum alloy (such as <0.6%), the greater the affinity between the aluminum alloy liquid and the mold steel, and the more likely it is to stick to the mold. Appropriately increasing the iron content of the aluminum alloy liquid can better reduce the adhesion of the aluminum alloy to the mold; it is generally required that the iron content in the die-casting aluminum alloy liquid be controlled at 0.6% to 0.95%. It is necessary to prevent mold sticking caused by mixing with low melting point metals. When using a master alloy to adjust the chemical composition, in addition to individual metals such as magnesium and zinc, pure metals cannot be added to the aluminum liquid to prevent severe segregation from causing mold sticking.
The greater the shrinkage of the die-casting alloy, not only the easier it is to stick to the mold, but also the worse the high-temperature strength. Some alloys have a larger shrinkage rate; the wider the liquid and solid phase temperature range of the alloy, the greater the shrinkage of the alloy. According to the structural shape and complexity of the casting, if the mold sticking and deformation caused by shrinkage are difficult to eliminate, consider switching to an alloy with small body shrinkage and linear shrinkage and high high-temperature strength; or adjust the alloy composition (such as aluminum). When the silicon content in the silicon alloy increases, the shrinkage rate of the casting becomes smaller) to reduce the shrinkage rate; or to modify the alloy, add 0.15% to 0.2% of metal titanium and other grain refiners to the aluminum alloy liquid to reduce the alloy The tendency to shrink.
4 Conclusion
There are many reasons for the sticking of die castings, and the measures to solve sticking are also different. The article specifically proposes measures to solve the sticking defects of die castings. We should carefully observe and analyze the reasons for sticking, and take targeted measures. Corresponding countermeasures can effectively solve the problem of mold sticking.
Please keep the source and address of this article for reprinting: The Concrete Measures To Solve The Sticky Mold Defects Of Die Casting
Minghe Casting Company are dedicated to manufacture and provide quality and high performance Casting Parts(metal die casting parts range mainly include Thin-Wall Die Casting,Hot Chamber Die Casting,Cold Chamber Die Casting),Round Service(Die Casting Service,Cnc Machining,Mold Making,Surface Treatment).Any custom Aluminum die casting, magnesium or Zamak/zinc die casting and other castings requirements are welcome to contact us.
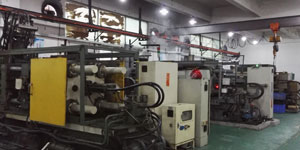
Under the control of ISO9001 and TS 16949,All processes are carried out through hundreds of advanced die casting machines, 5-axis machines, and other facilities, ranging from blasters to Ultra Sonic washing machines.Minghe not only has advanced equipment but also have professional team of experienced engineers,operators and inspectors to make the customer’s design come true.
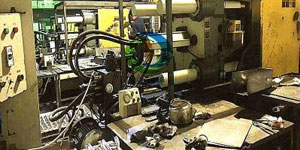
Contract manufacturer of die castings. Capabilities include cold chamber aluminum die casting parts from 0.15 lbs. to 6 lbs., quick change set up, and machining. Value-added services include polishing, vibrating, deburring, shot blasting, painting, plating, coating, assembly, and tooling. Materials worked with include alloys such as 360, 380, 383, and 413.
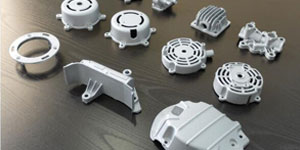
Zinc die casting design assistance/concurrent engineering services. Custom manufacturer of precision zinc die castings. Miniature castings, high pressure die castings, multi-slide mold castings, conventional mold castings, unit die and independent die castings and cavity sealed castings can be manufactured. Castings can be manufactured in lengths and widths up to 24 in. in +/-0.0005 in. tolerance.
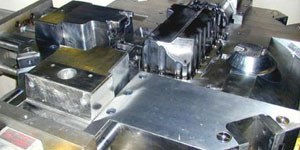
ISO 9001: 2015 certified manufacturer of die cast magnesium, Capabilities include high-pressure magnesium die casting up to 200 ton hot chamber & 3000 ton cold chamber, tooling design, polishing, molding, machining, powder & liquid painting, full QA with CMM capabilities, assembly, packaging & delivery.
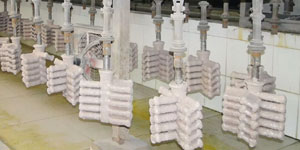
ITAF16949 certified. Additional Casting Service Include investment casting,sand casting,Gravity Casting, Lost Foam Casting,Centrifugal Casting,Vacuum Casting,Permanent Mold Casting,.Capabilities include EDI, engineering assistance, solid modeling and secondary processing.
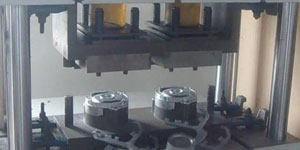
Casting Industries Parts Case Studies for: Cars, Bikes, Aircraft, Musical instruments, Watercraft, Optical devices, Sensors, Models, Electronic devices, Enclosures, Clocks, Machinery, Engines, Furniture, Jewelry, Jigs, Telecom, Lighting, Medical devices, Photographic devices, Robots, Sculptures, Sound equipment, Sporting equipment, Tooling, Toys and more.
What Can we help you do next?
∇ Go To Homepage For Die Casting China
→Casting Parts-Find out what we have done.
→Ralated Tips About Die Casting Services
By Minghe Die Casting Manufacturer |Categories: Helpful Articles |Material Tags: Aluminum Casting, Zinc Casting, Magnesium Casting, Titanium Casting, Stainless Steel Casting, Brass Casting,Bronze Casting,Casting Video,Company History,Aluminum Die Casting |Comments Off
Link to this article:The Concrete Measures To Solve The Sticky Mold Defects Of Die Casting
Reprint Statement: If there are no special instructions, all articles on this site are original. Please indicate the source for reprinting.:Cut Wiki,Thanks!^^