The use of powder metallurgy (P / M) process to manufacture parts for automotive power systems continues to grow. Parts manufactured by P / M process have many important and unique advantages. The residual porous structure intentionally left in these parts is good for self lubrication and sound insulation. Complex alloys that are difficult or impossible to manufacture by traditional casting process can be produced by using P / M technology. Parts manufactured by this technology usually have little or no processing capacity, which makes them cheaper and less waste in materials. Unfortunately, behind the attraction of these features, P / M parts are difficult to machine.
Although one of the original intentions of the P / M industry is to eliminate all processing, this goal has not yet been achieved. Most parts can only be “close to the final shape” and still need some finishing.
However, compared with castings and forgings, a small amount of material that needs to be removed from P / M parts is a typical wear-resistant material.
Porous structure is one of the characteristics that make p / M parts have a wide range of uses, but the tool life will also be damaged by porous structure. Porous structure can store oil and sound, but it also leads to micro intermittent cutting. When moving back and forth from the hole to the solid particles, the tool tip is continuously impacted, which can lead to very small fatigue fracture deformation and fine edge collapse along the cutting edge. To make matters worse, the particles are usually very hard. Even if the macro hardness of the material measured is between 20 and 35 degrees, the particle size of the component is as high as 60 degrees. These hard particles cause severe and rapid edge wear. Many p / M parts are heat treatable, and the hardness and strength of the material are higher after heat treatment. Finally, due to the sintering and heat treatment technology and the gases used, the surface of the material will contain hard and wear-resistant oxides and / or carbides.
Performance of P / M parts
Most of the properties of P / M parts, including machinability, are related not only to the chemical composition of the alloy, but also to the porosity level of the porous structure. The porosity of many structural parts is up to 15% ~ 20%. The porosity of parts used as filtration devices may be as high as 50%. At the other end of the series, the porosity of forged or hip parts is only 1% or less. These materials are becoming particularly important in automotive and aircraft applications because they can achieve higher levels of strength.
The tensile strength, toughness and ductility of P / M alloy will increase with the increase of density, and the machinability may also be improved, because the porosity is harmful to the tool tip.
The increase of porosity level can improve the sound insulation performance of parts. The damping oscillation in standard parts is significantly reduced in P / M parts, which is very important for machine tools, air conditioning blowpipes and pneumatic tools. High porosity is also necessary for self-lubricating gears.
Difficulties in machining
Although one of the goals of the continuous development of P / M industry is to eliminate machining, and one of the main attractions of P / M process is that only a small amount of processing is needed, many parts still need post-treatment to obtain higher accuracy or better surface finish. Unfortunately, machining these parts is extremely difficult. Most of the problems encountered are caused by porosity. Porosity leads to micro fatigue of the cutting edge. The cutting edge is constantly cutting in and out. It passes between particles and holes. Repeated small impact leads to small cracks on the cutting edge.
These fatigue cracks grow until the cutting edge collapses. This kind of micro chipping edge is usually very small, and usually shows normal abrasive wear.
Porosity also reduces the thermal conductivity of P / M parts, which results in high temperature on the cutting edge and causes crater wear and deformation. The internally connected porous structure provides a path for the discharge of cutting fluid from the cutting area. This can cause hot cracks or deformation, especially in drilling.
The increase of surface area caused by internal porous structure also leads to oxidation and / or carbonization during heat treatment. As mentioned earlier, these oxides and carbides are hard and wear-resistant.
The porous structure also gives the failure of the part hardness reading, which is extremely important. When the macro hardness of a P / M part is measured intentionally, it includes the factor of hole hardness. The porous structure leads to the collapse of the structure and gives the wrong impression of relatively soft parts. The particles are much harder. As described above, the difference is dramatic.
The existence of inclusions in PM parts is also disadvantageous. During machining, these particles will be pulled up from the surface, and scratch or scratch will be formed on the surface of the part when it is rubbed in front of the tool. These inclusions are usually large, leaving visible holes on the surface of the part.
The difference of carbon content leads to the inconsistency of machinability. For example, the carbon content of fc0208 alloy ranges from 0.6% to 0.9%. A batch of materials with 0.9% carbon content are relatively hard, resulting in poor tool life. The other batch of materials with 0.6% carbon content have excellent tool life. Both alloys are within the allowable range.
The final machining problem is related to the type of cutting that occurs on the P / M part. As the part is close to the final shape, the cutting depth is usually very shallow. This requires a free cutting edge. Chip build-up on the cutting edge often leads to micro chipping.
Processing technology
To overcome these problems, several technologies (unique to the industry) are applied. The surface porous structure is often sealed by infiltration. Additional free cutting is usually required. Recently, improved powder production techniques designed to increase powder cleanliness and reduce oxides and carbides during heat treatment have been used.
The closed surface porous structure is accomplished by metal (usually copper) or polymer infiltration. It has been speculated that infiltration acts as a lubricant. Most of the experimental data show that the real advantage lies in closing the surface porous structure and thus preventing the micro fatigue of the cutting edge. The reduction of chatter improves tool life and surface finish. The most dramatic use of infiltration shows a 200% increase in tool life when the porous structure is closed.
Additives such as MNS, s, MoS2, MgSiO3 and BN are known to increase tool life. These additives improve machinability by making it easier for chips to separate from the workpiece, breaking chips, preventing chip build-up and lubricating the cutting edge. Increasing the amount of additives can improve the machinability, but reduce the strength and toughness.
Powder atomization technology to control sintering and heat treatment furnace gas makes it possible to produce clean powder and parts, which minimizes the occurrence of inclusions and surface oxide carbides.
Tool material
The most widely used tools in P / M industry are those materials which are wear-resistant, edge crack resistant and chip free under the condition of good surface finish. These characteristics are useful for any machining operation, especially for P / M parts. The tool materials included in this category are cubic boron nitride (CBN) tools, uncoated and coated cermets, and improved coated sintered cemented carbides.
CBN tools are attractive because of their high hardness and wear resistance. This tool has been used for many years in the processing of steel and cast iron with Rockwell hardness of 45 and above. However, due to the unique properties of P / M alloy and the significant difference between microhardness and macrohardness, CBN tools can be used for P / M parts with Rockwell hardness of 25. The key parameter is the hardness of particles. When the hardness of particles exceeds Rockwell 50 degrees, CBN tools are available regardless of the macro hardness value. The obvious limitation of these tools is their lack of toughness. In case of intermittent cutting or high porosity, edge reinforcement including negative chamfering and heavy honing is necessary. Simple light cutting can be done with honed cutting edge.
There are several materials of CBN that are effective. The material with the best toughness is mainly composed of the whole CBN. They have excellent toughness, so they can be used for roughing. Their limitations are usually related to the surface finish. It is largely determined by the individual CBN particles that make up the tool. When the particles fall off from the cutting edge, they will affect the surface of the workpiece material. However, it is not so serious that the fine particle tool falls off one particle.
The CBN material usually used has high content of CBN and medium particle size. CBN finishing blade is fine grain, and CBN content is low. They are most effective when light cutting and surface finish are required or when the alloy being processed is particularly hard.
In many cutting applications, tool life is independent of material type. In other words, any CBN material can achieve similar tool life. In these cases, the material selection is mainly based on the lowest cost of each cutting edge. One round blade has a whole CBN top surface and can provide four or more cutting edges, which is cheaper than four inlaid CBN blades.
When the hardness of P / M parts is lower than Rockwell 35 degree, and the hardness of particles is within the range, cermet is usually one of the choices. Cermets are very hard, can effectively prevent chip build-up and can withstand high speed. In addition, because cermets have always been used for high-speed and finish machining of steel and stainless steel, they usually have ideal geometric grooves suitable for close to formed parts.
Today’s cermets are intricate in metallurgy, with up to 11 alloying elements. They are usually sintered from TiCN particles and Ni Mo adhesive. TiCN provides hardness, chip build-up resistance and chemical stability that are important for the successful use of cermets. In addition, these tools usually have a high adhesive content, which means they have good toughness. In a word, they have all the characteristics of processing P / M alloy effectively. Several kinds of cermets are effective, just like tungsten carbide sintered cemented carbide, the higher the content of binder, the better the toughness.
A known relatively new development is that medium temperature chemical vapor deposition (mtcvd) also provides an advantage for the P / M industry. Mtcvd retains all the wear resistance and crater wear resistance of the traditional chemical vapor deposition (CVD), but also improves the toughness objectively. The increase of toughness mainly comes from the decrease of cracks. The coating is deposited at high temperature and then cooled in the furnace. The coating contains cracks when the tool reaches room temperature due to inconsistent thermal expansion. Similar to scratches on flat glass, these cracks reduce the strength of the cutting edge. The lower deposition temperature of mtcvd leads to lower crack frequency and better toughness of cutting edge.
When the substrate of CVD coating and mtcvd coating have the same characteristics and edge dressing, the difference of their toughness can be demonstrated. When used in applications where edge toughness is required, the performance of mtcvd coating is better than that of CVD coating. Through analysis, when machining P / M parts with porous structure, the edge toughness is important. Mtcvd coating is better than CVD coating.
The physical vapor deposition (PVD) coating is thinner and less wear resistant than mtcvd or CVD coating. However, PVD coating can withstand significant impact in application. PVD coating is effective when cutting is abrasive wear, CBN and cermets are too brittle and require excellent surface finish.
For example, the cutting edge of C-2 cemented carbide can be machined fc0205 at a line speed of 180 m / min and a feed rate of 0.15 mm / revolution. After machining 20 parts, the chip build-up can cause micro collapse. When PVD titanium nitride (TIN) coating is used, chip build-up is restrained and tool life is prolonged. When tin coating is used for this test, the abrasive wear characteristics of P / M parts are expected to be more effective with TiCN coating. TiCN has almost the same chip build-up resistance as tin, but it is harder and more wear-resistant than tin.
Porous structure is important and it affects the machinability of fc0208 alloy. When the porous structure and characteristics change, different tool materials provide corresponding advantages. When the density is low (6.4g/cm3), the macrohardness is low. In this case, mtcvd coated cemented carbide provides the best tool life. The micro fatigue of cutting edge is very important, and the edge toughness is very important. In this case, a good toughness cermet blade provides the maximum tool life.
When producing the same alloy with a density of 6.8g/cm3, abrasive wear becomes more important than edge crack. In this case, mtcvd coating provides the best tool life. PVD coated cemented carbide is used to test the two types of extremely hard parts, and it breaks when it touches the cutting edge.
When the speed increases (the linear speed is more than 300 meters per minute), cermets and even coated cermets will produce crater wear. Coated cemented carbide is more suitable, especially when the cutting edge toughness of coated cemented carbide is good. Mtcvd coating is especially effective for cemented carbide with cobalt rich area.
Cermets are most commonly used in turning and boring. PVD coated cemented carbides are ideal for thread machining because lower speeds and more attention to build-up may be expected.
Please keep the source and address of this article for reprinting:Cutting Machining Of Powder Metallurgy (P/M) Parts
Minghe Casting Company are dedicated to manufacture and provide quality and high performance Casting Parts(metal die casting parts range mainly include Thin-Wall Die Casting,Hot Chamber Die Casting,Cold Chamber Die Casting),Round Service(Die Casting Service,Cnc Machining,Mold Making,Surface Treatment).Any custom Aluminum die casting, magnesium or Zamak/zinc die casting and other castings requirements are welcome to contact us.
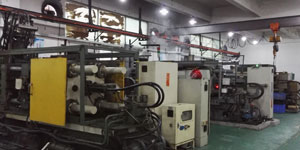
Under the control of ISO9001 and TS 16949,All processes are carried out through hundreds of advanced die casting machines, 5-axis machines, and other facilities, ranging from blasters to Ultra Sonic washing machines.Minghe not only has advanced equipment but also have professional team of experienced engineers,operators and inspectors to make the customer’s design come true.
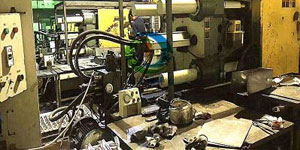
Contract manufacturer of die castings. Capabilities include cold chamber aluminum die casting parts from 0.15 lbs. to 6 lbs., quick change set up, and machining. Value-added services include polishing, vibrating, deburring, shot blasting, painting, plating, coating, assembly, and tooling. Materials worked with include alloys such as 360, 380, 383, and 413.
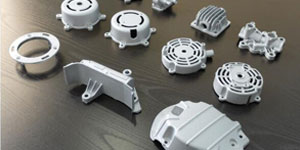
Zinc die casting design assistance/concurrent engineering services. Custom manufacturer of precision zinc die castings. Miniature castings, high pressure die castings, multi-slide mold castings, conventional mold castings, unit die and independent die castings and cavity sealed castings can be manufactured. Castings can be manufactured in lengths and widths up to 24 in. in +/-0.0005 in. tolerance.
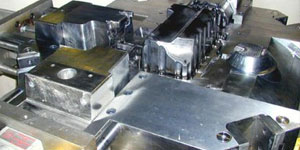
ISO 9001: 2015 certified manufacturer of die cast magnesium, Capabilities include high-pressure magnesium die casting up to 200 ton hot chamber & 3000 ton cold chamber, tooling design, polishing, molding, machining, powder & liquid painting, full QA with CMM capabilities, assembly, packaging & delivery.
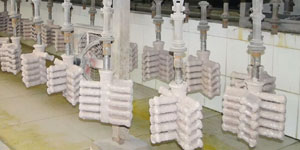
ITAF16949 certified. Additional Casting Service Include investment casting,sand casting,Gravity Casting, Lost Foam Casting,Centrifugal Casting,Vacuum Casting,Permanent Mold Casting,.Capabilities include EDI, engineering assistance, solid modeling and secondary processing.
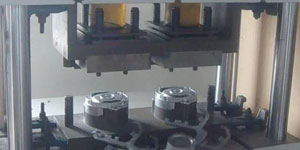
Casting Industries Parts Case Studies for: Cars, Bikes, Aircraft, Musical instruments, Watercraft, Optical devices, Sensors, Models, Electronic devices, Enclosures, Clocks, Machinery, Engines, Furniture, Jewelry, Jigs, Telecom, Lighting, Medical devices, Photographic devices, Robots, Sculptures, Sound equipment, Sporting equipment, Tooling, Toys and more.
What Can we help you do next?
∇ Go To Homepage For Die Casting China
→Casting Parts-Find out what we have done.
→Ralated Tips About Die Casting Services
By Minghe Die Casting Manufacturer |Categories: Helpful Articles |Material Tags: Aluminum Casting, Zinc Casting, Magnesium Casting, Titanium Casting, Stainless Steel Casting, Brass Casting,Bronze Casting,Casting Video,Company History,Aluminum Die Casting |Comments Off
Link to this article:Cutting Machining Of Powder Metallurgy (P/M) Parts
Reprint Statement: If there are no special instructions, all articles on this site are original. Please indicate the source for reprinting.:Cut Wiki,Thanks!^^